1、 Why the circuit board is required to be very flat
In the automatic plug-in line, if the printed circuit board is not flat, it will cause inaccuracy. Components cannot be inserted into the holes and surface mount pads of the board, and even the automatic plug-in machine will be damaged. The circuit board with components is bent after welding, so it is difficult to cut the component feet in order. The circuit board can't be installed on the box or the socket inside the machine, so the circuit board factory is also very upset when it encounters the board warpage. At present, printed circuit board has entered the era of surface mounting and chip mounting, and the requirements of board warping must be more and more strict.
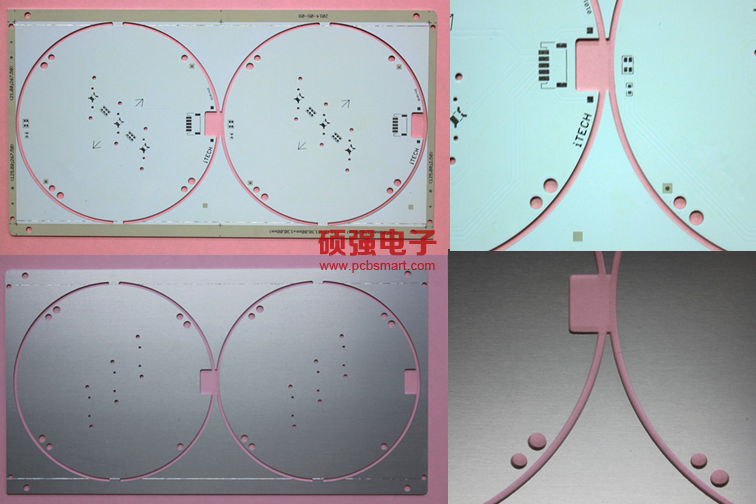
2、 Standard and test method of warpage
According to ipc-6012 (1996 edition) (identification and Performance Specification for rigid printed circuit boards), the maximum allowable warpage and twist for surface mounted printed circuit boards is 0.75%, and for other boards is 1.5%. Compared with ipc-rb-276 (1992 edition), the requirements for surface mounted printed circuit boards are improved. At present, the allowable warpage of each electronic assembly plant, no matter the double-sided circuit board or multi-layer circuit board, is 1.6mm thick, usually 0.40-0.75%. Many SMT and BGA boards require 0.3%. Some electronic factories are agitating to raise the standard of warpage to 0.2%, and the test method of warpage shall comply with gb4677.5-84 or ipc-tm-650.2.4.22b. Put the printed circuit board on the verified platform, insert the test needle to the place with the largest warpage, divide the diameter of the test needle by the length of the curved edge of the printed circuit board, and then calculate the warpage of the printed circuit board.
3、 Warpage of anti plate during manufacturing
1. Engineering design: precautions for PCB Design:
A. Multi layer PCB core board and semi curing sheet shall use products of the same supplier.
B. The arrangement of interlaminar prepreg should be symmetrical, for example, the thickness of 1-2 and 5-6 interlaminar should be the same as the number of prepreg sheets, otherwise it is easy to warp after lamination.
C. The line graphic area of outer layer a and B shall be as close as possible. If a side is a large copper side, and B side only a few wires, this printed board after etching is easy to warp. If the line area difference between the two sides is too large, some independent grids can be added on the sparse side for balance.
2. Drying plate before blanking:
The purpose of baking the copper clad laminate before blanking (150 ℃, 8 ± 2 hours) is to remove the moisture in the laminate, at the same time, make the resin in the laminate fully solidified, and further eliminate the residual stress in the laminate, which is helpful to prevent the warpage of the laminate. At present, many double-sided circuit boards and multi-layer circuit boards still adhere to the step of baking before or after blanking. However, there are exceptions in some board factories. At present, the baking time of PCB factories is not the same, from 4 to 10 hours. It is recommended to determine according to the grade of printed boards produced and the requirements of customers for warpage. The two methods are feasible. It is suggested to dry the panel after cutting. The inner layer should also be baked.
3. The longitudinal and latitudinal directions of the prepreg:
After laminating, the shrinkage of the semi-cured sheet is different in warp and weft directions. It is necessary to distinguish the warp and weft directions when blanking and laminating. Otherwise, it is easy to cause warpage of the finished plate after lamination, and it is difficult to correct even if the pressure is applied to bake the plate. Many of the reasons for the warpage of the multi-layer board are caused by the unclear longitude and latitude direction of the semi curing sheet during lamination and the disorderly stacking.
How to distinguish longitude and latitude? The winding direction of the rolled semi-cured sheet is longitude, while the width direction is latitude; for copper foil, the long side is longitude, and the short side is longitude. If you are not sure, you can inquire the PCB manufacturer or supplier.
4. Stress removal after lamination:
After the hot pressing and cold pressing, the multilayer circuit board is taken out, the burr is cut or milled off, and then it is dried in an oven at 150 ℃ for 4 hours, so as to gradually release the stress in the board and completely cure the resin. This step cannot be omitted.
5. The thin plate needs to be straightened during electroplating:
Special nipping roller shall be made for 0.6-0.8mm thin multilayer circuit board for plate surface electroplating and graphic electroplating. After nipping the thin plate on the flying bar on the automatic electroplating line, a round stick shall be used to string the nipping roller on the whole flying bar, so as to straighten all the plates on the roll, so that the plate after electroplating will not deform. Without this measure, after plating the copper layer of 20 or 30 microns, the sheet will bend and be difficult to remedy.
6. Cooling of the plate after hot air leveling:
During the hot air leveling of PCB, it will be impacted by the high temperature of solder bath (about 250 ℃), and it shall be placed on the flat marble or steel plate for natural cooling after being taken out, and then sent to the post processor for cleaning. This is good for anti warping board. In some PCB factories, in order to enhance the brightness of the lead tin surface, the board is put into cold water immediately after hot air leveling, and taken out after a few seconds for post-treatment. This kind of hot cold impact is likely to cause warpage, stratification or blistering on some types of boards. In addition, air floating bed can be installed on the equipment for cooling.
7. Treatment of warping board:
The PCB Factory with orderly management will conduct 100% flatness inspection at the final inspection. All unqualified plates will be picked out and put into the oven. Bake at 150 ℃ and under heavy pressure for 3-6 hours, and cool naturally under heavy pressure. Then take out the board by pressure relief, and check the flatness. In this way, some boards can be saved. Some boards can only be leveled after two or three times of baking. Shenzhen youlutong Technology Co., Ltd. has a very good effect in using to remedy circuit board warpage. If the above-mentioned anti warping process measures are not implemented, some circuit boards are useless for drying and pressing, and can only be scrapped.